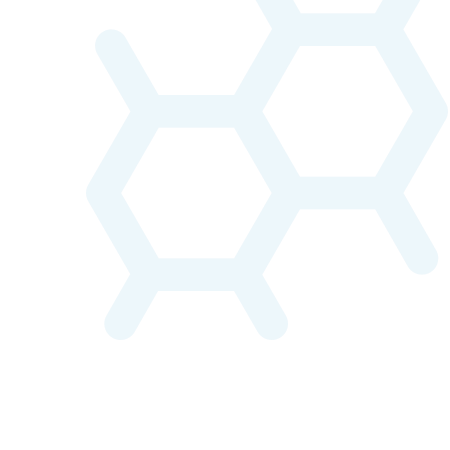
Magnet Coatings
Bonded Neo (MQ1™) magnets are generally coated prior to being delivered to a magnet user. Typically, MQ1™ magnets are coated via an Electrophoresis Coating or Spray Coating method. However, other coatings and coating methods are available if your magnet requires a particular characteristic or operates in a particularly high temperature or corrosive environment.
The following table summarizes a few of the options available along with key attributes of each.
Should you have any questions about which coating is right for your application, please contact us.
Coating type | Details | Salt Spray Test Results (35°C*5%NaCI) | PCT Test Results (120°C*95RH%*2atm) | Description |
---|---|---|---|---|
Electrophoresis Coating ("E-coating") | ~20µm | ~100hrs | ~10hrs | E-coating is the most common coating for MQ1™ magnets; it provides uniform coating thickness and is suitable for many applications |
Spray coating | ~10µm | ~30hrs | ** | Spray coating is a common coating method for MQ1™ magnets; it is better suited for smaller magnets which are not exposed to corrosive environments |
Parylene coating | ~10µm | ~50hrs | ~170hrs | Parylene can be used in applications which experience corrosive environments, such as water Parylene coating performs especially well in Salt Spray and PCT Tests |
~30µm | ~250hrs | ~250hrs | ||
Dipping | ~5µm | ~10hrs | ** | Dipping is not a commonly used coating for MQ1™ magnets; the coating is relatively thin, rendering its corrosion protection characteristics rather poor |
Nickel Plating ("Ni-Plating") | ~20µm | ~30hrs | ~120hrs | While nickel coating is widely used for fully dense sintered magnets, it is not a very common coating for MQ1™ magnets, as the adhesion between the magnet and the nickel plating is not optimal. It is used only in certain applications |
** Test not performed for these coatings due to poor results